Introduction
Lean management is a philosophy that’s long been lauded for its ability to improve efficiency and eliminate waste in various business processes. Originally formulated in the automotive industry, it’s now found relevance in diverse fields, including the intricate world of supply chain management. In this article, we’ll explore the principles of lean management and how they can be practically applied in your supply chain operations to deliver enhanced value.
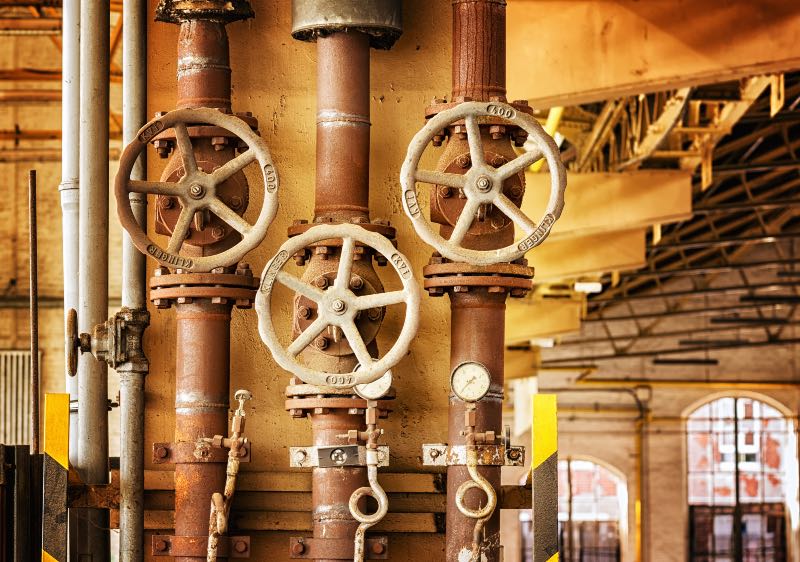
Understanding Lean Principles
Lean management originated from the Japanese manufacturing industry, specifically from the Toyota Production System. At its core, it aims to create more value for customers by optimizing resources, eliminating waste, and improving efficiency. The five principles of lean, as identified by James Womack and Daniel Jones in their book “Lean Thinking,” are:
- Value: Define what value the customer is gaining from the product or service.
- Value Stream: Identify all the steps in the value stream and eliminate any wasteful steps.
- Flow: Ensure the remaining steps run smoothly without interruption or delay.
- Pull: Customers pull value from the producer.
- Perfection: Seek constant improvement to create more value with less waste.
The lean philosophy is not just a set of tools or methods for process improvement, but it requires a change in culture and mindset toward continuous improvement and respect for people.
Lean Principles in the Supply Chain Context
Applying lean principles in the context of supply chain management involves reducing waste and improving efficiency across the entire supply chain network, from raw material suppliers to end customers. Here’s how the lean principles can be adapted:
- Value: In supply chain management, value is determined by what customers are willing to pay for. Understanding customer value is crucial to decide which activities are valuable and which are wasteful in the supply chain.
- Value Stream: This involves mapping all processes involved in the production and delivery of products or services and identifying areas of waste.
- Flow: Here, the goal is to ensure a seamless flow of products, information, and funds across the supply chain, eliminating delays and interruptions.
- Pull: In a lean supply chain, production is based on actual customer demand rather than forecasted demand, thereby reducing overproduction and inventory costs.
- Perfection: This principle drives the continuous search for ways to improve processes and eliminate waste in the supply chain.
Practical Implementation of Lean Principles in Your Supply Chain
Adopting lean principles in your supply chain operations requires a systematic approach. Here’s how you can implement lean thinking:
- Understand Customer Value: Start by identifying what your customers value most. It could be faster delivery times, lower prices, superior quality, or any other factor.
- Map Your Value Stream: Document every step in your supply chain process – from procurement of raw materials to the delivery of final products. This helps in visualizing the process and identifying non-value adding activities.
- Identify and Eliminate Waste: Waste in the supply chain can be in many forms, including overproduction, waiting time, transport, over-processing, inventory, unnecessary motion, and defects. Use lean tools like 5S, kaizen, or value stream mapping to uncover and eliminate these wastes.
- Ensure Smooth Flow: Streamline processes and remove bottlenecks to ensure a smooth flow of materials, information, and finances. Techniques such as ‘Just-in-time’ (JIT) can be used to manage inventory efficiently and reduce lead times.
- Implement a Pull System: A pull system is demand-driven, meaning production is initiated based on actual customer demand rather than forecasts. This can help avoid overproduction and reduce inventory holding costs. Kanban is a well-known method used to implement a pull system.
- Pursue Perfection: Strive for continuous improvement in your supply chain operations. Regular audits, employee training, and maintaining open lines of communication can all contribute to a culture of continuous improvement.
Advantages of Going Lean
Going lean can offer numerous benefits to supply chain operations:
- Reduced Waste: The main objective of lean is to reduce waste. By identifying non-value-adding activities and eliminating them, companies can significantly cut costs.
- Improved Efficiency: Streamlining processes and reducing interruptions leads to more efficient operations and faster delivery times.
- Better Quality: Lean principles focus on doing it right the first time, which leads to better quality products and fewer defects.
- Improved Customer Satisfaction: Faster delivery, better quality, and lower costs all contribute to enhanced customer satisfaction and loyalty.
Challenges in Implementing Lean Principles
While lean principles offer substantial benefits, implementing them isn’t without challenges. It requires a shift in culture and mindset, which can be difficult to achieve. Overcoming resistance to change, training employees, and maintaining the momentum of continuous improvement can be demanding. However, with strong leadership and consistent effort, these challenges can be overcome.
Case Study: How Toyota Successfully Implemented Lean Principles
To see lean principles in action, look no further than Toyota, the company where it all started. The Toyota Production System (TPS), characterized by its lean manufacturing principles, is widely studied and replicated. Toyota implemented lean principles through continuous improvement (Kaizen), respect for people, and long-term thinking. This system helped Toyota reduce waste, improve efficiency, and become a global leader in the automotive industry. You can read more about Toyota’s lean journey here.
Conclusion
Incorporating lean principles in your supply chain management can significantly improve efficiency, reduce waste, and enhance customer satisfaction. However, implementing lean is not a one-time task but a continuous journey. It requires a change in culture and constant vigilance to identify and eliminate waste in its many forms.
Another excellent resource to learn more about lean is the Lean Enterprise Institute (www.lean.org), where you’ll find a wealth of information on how to effectively implement lean principles in various business contexts.
By going lean, you’ll be well on your way to creating a more efficient, flexible, and cost-effective supply chain that delivers superior value to your customers.
Remember, “The most dangerous kind of waste is the waste we do not recognize.” – Shigeo Shingo, Toyota engineer and lean pioneer.
Lean Principles and Supply Chain: An In-Depth Look
Building on the foundation of lean thinking in the supply chain, it’s worthwhile to delve a bit deeper into the mechanics of lean principles and how they apply to different elements of the supply chain.
Supply Chain Design and Lean Thinking
When incorporating lean principles, supply chain design plays a pivotal role. Aligning your supply chain design with lean principles involves strategically placing suppliers, manufacturing facilities, warehouses, and distribution centers to reduce waste in transportation, overstocking, and delays. It also involves choosing partners who understand and align with your lean philosophy.
Sourcing and Lean Principles
Procuring raw materials and components is the first step in most supply chains. Implementing lean thinking here means sourcing from suppliers that provide high-quality materials promptly and consistently. It can also involve establishing long-term relationships with suppliers and assisting them in their lean journey to ensure a consistent, reliable flow of goods.
Production and Lean Thinking
Production processes are often the first target of lean initiatives. By focusing on creating flow and pull, reducing downtime, and continually improving processes, waste can be minimized, and productivity can be enhanced. The goal is to create systems that respond to customer demand efficiently without creating excess inventory or defects.
Logistics and Lean Principles
Applying lean to logistics involves optimizing transportation routes and schedules, consolidating shipments, and coordinating effectively with suppliers and customers. The goal is to ensure goods reach their destination as quickly and efficiently as possible, without unnecessary detours or delays.
Inventory Management and Lean Thinking
Inventory is a significant area of focus in lean supply chain management. Excess inventory ties up capital and occupies space, while too little can disrupt production and lead to lost sales. Techniques like Just-in-Time (JIT) delivery, continuous replenishment, and vendor-managed inventory (VMI) can help balance the need for availability against the desire to minimize waste.
Lean Leadership in Supply Chain Management
Implementing lean principles in the supply chain isn’t just a matter of tools and techniques – it’s also about leadership. Lean leaders lead by example, promote a culture of continuous improvement, and empower their teams to identify and eliminate waste. They also understand that lean is about more than cost-cutting – it’s about delivering value to customers and creating a sustainable, efficient business.
Conclusion: Going Beyond Lean
While lean principles provide a strong foundation for efficient, waste-free operations, many organizations are now going beyond lean to incorporate concepts like agility and resilience into their supply chains. However, these do not replace lean but rather build on its foundation.
For example, an agile supply chain is one that can quickly respond to changes in demand or supply, while a resilient supply chain can withstand disruptions and quickly return to normal operations. Both of these concepts rely on lean principles like flow, pull, and continuous improvement to be effective.
In the final analysis, lean principles offer a proven framework for improving supply chain efficiency and effectiveness. But the lean journey doesn’t end with the implementation of these principles – it’s a continuous journey of learning, improvement, and adaptation to meet the changing needs of customers and the business environment. As you continue your lean journey, always keep in mind the ultimate goal: to create more value for customers, with less waste and effort.
Recommended further reading: “The Machine That Changed the World” by James P. Womack, Daniel T. Jones, and Daniel Roos, which provides an excellent overview of lean principles and their application in various industries. You can find it here.
For more info on implementing a Just-In-Time (JIT) inventory management system, please read our article: http://supplychaintoolbox.com/inventory-supply-chain-management/how-to-implement-just-in-time-jit-inventory-management/
Geef een reactie