Introduction
Effectively managing a supply chain requires tracking key performance indicators (KPIs) that can provide valuable insights into the overall performance and efficiency of your operations. In this article, we will discuss the top 5 supply chain metrics every business should track, provide a relevant case study, and outline best practices for setting up a metrics system. Additionally, we will recommend resources to enhance your understanding of supply chain management, including helpful links to SupplyChainToolbox.com.
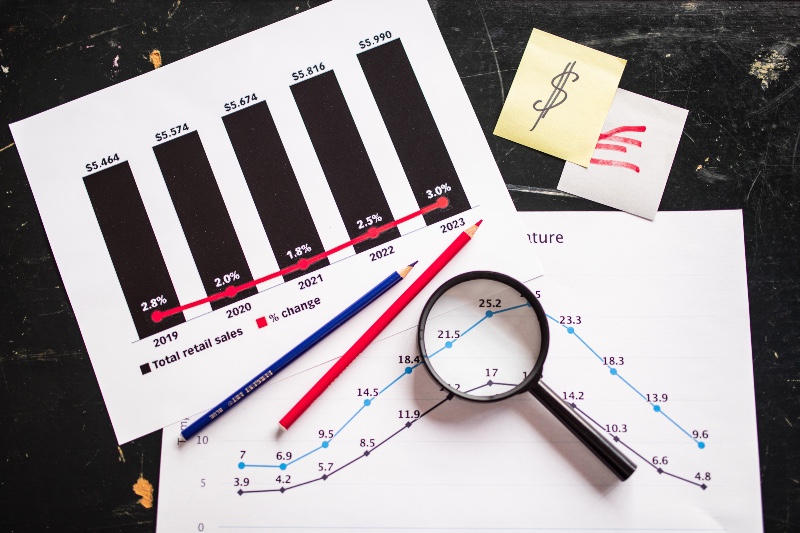
On-Time Delivery
On-time delivery measures the percentage of orders delivered within the agreed-upon time frame. This metric is crucial for customer satisfaction and maintaining strong relationships with suppliers and partners. Regularly monitoring on-time delivery can help identify potential issues in your logistics processes and enable you to take corrective actions promptly. To calculate on-time delivery, divide the number of orders delivered on time by the total number of orders, then multiply the result by 100 to get the percentage.
Inventory Turnover
Inventory turnover is the number of times a company sells and replaces its inventory during a specific period. A high inventory turnover indicates efficient inventory management, while a low turnover may signify excess stock or slow-moving items. Tracking inventory turnover helps businesses optimize their inventory levels, reduce carrying costs, and improve cash flow. Inventory turnover is calculated by dividing the cost of goods sold (COGS) by the average inventory value during a specific period.
Order Cycle Time
Order cycle time measures the time it takes to fulfill an order, from receipt to delivery. Shorter cycle times are generally preferred, as they indicate efficient operations and faster order processing. By tracking this metric, businesses can identify bottlenecks and implement improvements to streamline their order fulfillment processes. To calculate order cycle time, determine the total time taken for all orders during a specific period, and then divide this by the total number of orders in that period.
Fill Rate
Fill rate is the percentage of customer orders that are fulfilled without any stockouts or backorders. A high fill rate indicates that a company is effectively managing its inventory levels and meeting customer demand. Monitoring fill rate can help businesses improve inventory management, reduce stockouts, and enhance customer satisfaction. Fill rate is calculated by dividing the number of items shipped without any stockouts or backorders by the total number of items ordered, then multiplying the result by 100 to get the percentage.
Return on Assets (ROA)
Return on Assets (ROA) Return on Assets (ROA) measures the efficiency with which a company uses its assets to generate profit. It is calculated by dividing net income by total assets. A higher ROA indicates that a company is utilizing its assets more effectively to generate profit. By tracking ROA, businesses can evaluate the efficiency of their supply chain operations and make informed decisions about investments in assets and resources.
Practical example Supply Chain metrics
Let’s consider a fictive company, GreenSupply Co., that produces and sells eco-friendly products. Here is some data for a specific period:
- Number of orders delivered on time: 800
- Total number of orders: 1,000
- Cost of Goods Sold (COGS): $500,000
- Beginning Inventory: $100,000
- Purchases: $400,000
- Ending Inventory: $150,000
- Total time taken for all orders: 10,000 hours
- Number of items shipped without stockouts or backorders: 4,800
- Total number of items ordered: 5,000
- Net Income: $200,000
- Total Assets: $1,000,000
Using this data, we can calculate the five supply chain metrics for GreenSupply Co.:
- On-Time Delivery: On-Time Delivery (%) = (800 / 1,000) x 100 = 80%
- Inventory Turnover: Inventory Turnover = $500,000 / (($100,000 + $150,000) / 2) = $500,000 / $125,000 = 4
- Order Cycle Time: Order Cycle Time = 10,000
- Fill Rate: Fill Rate (%) = (4,800 / 5,000) x 100 = 96%
- Return on Assets (ROA): Return on Assets = $200,000 / $1,000,000 = 0.2 or 20%
Based on these calculations, GreenSupply Co. has an on-time delivery rate of 80%, an inventory turnover of 4 times, an average order cycle time of 10 hours per order, a fill rate of 96%, and a return on assets of 20%. By tracking and analyzing these supply chain metrics, GreenSupply Co. can identify areas for improvement, make informed decisions, and optimize its supply chain operations.
Case Study: Zara
Zara, a leading fast-fashion retailer, is well-known for its efficient supply chain management. The company closely monitors its supply chain metrics, allowing it to quickly adapt to changing market trends and customer preferences. By maintaining short lead times, optimizing inventory turnover, and effectively managing order fulfillment, Zara can introduce new products to the market rapidly while minimizing stockouts and markdowns. The company’s success in tracking and optimizing supply chain metrics has been a significant factor in its global expansion and continued growth.
Best Practices for Setting Up a Supply Chain Metrics System
Identify Key Metrics: Determine the most critical metrics for your business, considering factors such as industry benchmarks, company objectives, and customer expectations. Focus on a manageable number of KPIs to avoid information overload and ensure that your team can effectively monitor and act on the data.
Establish Baselines and Targets: Set baselines for each metric to provide a starting point for measuring performance. Develop realistic targets based on industry benchmarks and your company’s historical performance. Regularly review and adjust these targets as needed to reflect changing market conditions and business objectives.
Implement Data Collection and Reporting Systems: Invest in supply chain management software or utilize manual systems to collect, analyze, and report on your supply chain metrics. Ensure that data is accurate, timely, and easily accessible to all relevant stakeholders.
Communicate and Educate: Clearly communicate the importance of supply chain metrics to your team and provide training on how to track and interpret the data. Encourage a data-driven culture that values continuous improvement and data-based decision-making.
Review and Adjust: Regularly review your supply chain metrics and use the insights gained to inform strategic decisions, identify areas for improvement, and drive continuous optimization.
Discover the latest trends and insights on supply chain metrics from https://www.gartner.com/en/supply-chain/trends/hierarchy-supply-chain-metrics
Conclusion
By tracking the top 5 supply chain metrics, businesses can gain valuable insights into their supply chain performance, identify areas for improvement, and make informed decisions to optimize operations. The Zara case study demonstrates how effective supply chain metrics tracking can contribute to a company’s success and growth. Implementing best practices for setting up a supply chain metrics system, along with utilizing valuable resources such as SupplyChainToolbox.com, can help businesses stay competitive and achieve their supply chain management goals.
For more information on warehouse Automation, please check out our article http://supplychaintoolbox.com/supply-chain-and-logistics/warehouse-automation-the-future-of-supply-chain-management/.
Geef een reactie